What is Porosity in Welding: Crucial Tips for Getting Flawless Welds
What is Porosity in Welding: Crucial Tips for Getting Flawless Welds
Blog Article
Porosity in Welding: Identifying Common Issues and Implementing Finest Practices for Avoidance
Porosity in welding is a pervasive concern that usually goes undetected up until it creates considerable issues with the integrity of welds. In this conversation, we will explore the vital variables adding to porosity formation, examine its damaging impacts on weld performance, and discuss the ideal methods that can be adopted to decrease porosity incident in welding procedures.
Typical Root Causes Of Porosity
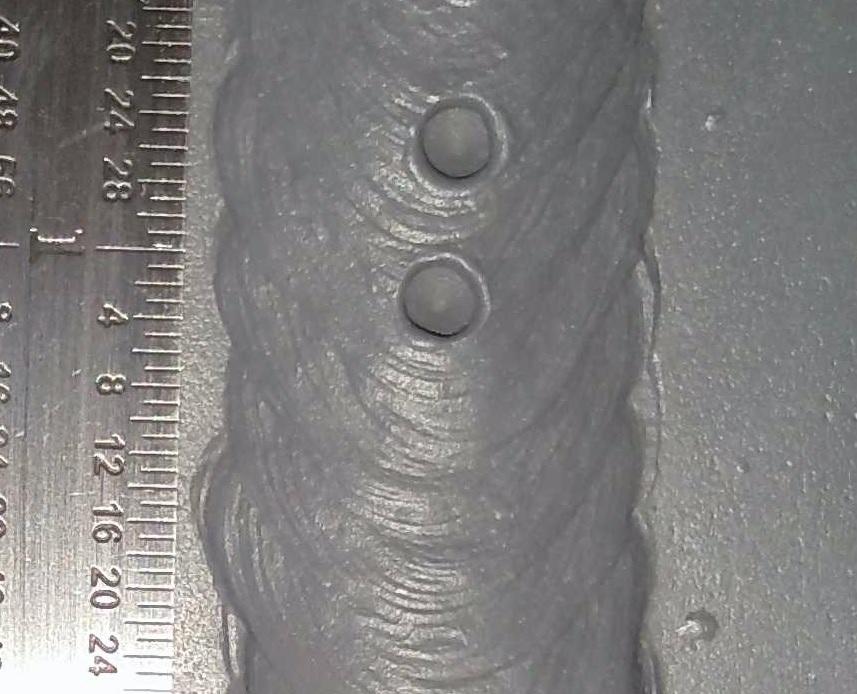
Another regular culprit behind porosity is the visibility of contaminants externally of the base metal, such as oil, grease, or rust. When these pollutants are not efficiently gotten rid of before welding, they can evaporate and end up being trapped in the weld, triggering defects. Furthermore, making use of unclean or wet filler products can introduce impurities into the weld, adding to porosity problems. To mitigate these common reasons for porosity, extensive cleaning of base steels, appropriate shielding gas selection, and adherence to optimal welding specifications are important practices in attaining premium, porosity-free welds.
Impact of Porosity on Weld Top Quality

The existence of porosity in welding can substantially jeopardize the structural integrity and mechanical buildings of welded joints. Porosity creates voids within the weld steel, damaging its total toughness and load-bearing capability. These spaces act as anxiety concentration points, making the weld extra vulnerable to cracking and failure under used tons. Furthermore, porosity can lower the weld's resistance to deterioration and various other ecological factors, further diminishing its durability and performance.
One of the primary repercussions of porosity is a reduction in the weld's ductility and sturdiness. Welds with high porosity degrees often tend to show lower effect strength and reduced capability to deform plastically before fracturing. This can be specifically concerning in applications where the welded components are subjected to vibrant or cyclic loading problems. Porosity can restrain the weld's ability to successfully transmit forces, leading to early weld failure and potential safety risks in important structures. What is Porosity.
Ideal Practices for Porosity Prevention
To boost the architectural stability and high quality of welded joints, what specific measures can be carried out to lessen the event of porosity during the welding process? Making use of the proper welding method for the certain material being welded, such as readjusting the welding angle and her latest blog weapon setting, can even more prevent porosity. Routine evaluation of welds and immediate removal of any type of problems identified throughout the welding process are important practices to protect against porosity and generate top notch welds.
Significance of Correct Welding Strategies
Applying appropriate welding strategies is paramount in making sure the architectural integrity and high quality of bonded joints, building upon the foundation of reliable porosity avoidance steps. Extreme warm can lead to raised porosity due to the entrapment of gases in the weld pool. Furthermore, making use of the appropriate welding specifications, such as voltage, present, and take a trip rate, is essential for accomplishing audio welds with marginal porosity.
Furthermore, the option of welding process, whether it be MIG, TIG, or stick welding, must straighten with the details requirements of the project to make sure ideal outcomes. Correct cleansing and preparation of the base metal, as well as choosing the best filler product, are likewise crucial parts of competent welding methods. By sticking to these ideal techniques, welders can decrease the threat of porosity click over here now development and generate top quality, structurally sound welds.

Checking and Quality Control Steps
Testing treatments are essential to detect and prevent porosity in welding, ensuring the strength and durability of the final product. Non-destructive testing approaches such as ultrasonic screening, radiographic screening, and visual evaluation are commonly employed to recognize possible flaws like porosity.
Post-weld examinations, on the other hand, examine the last weld for any type of flaws, consisting of porosity, and confirm that it fulfills specified requirements. Applying an extensive high quality control strategy that includes detailed testing procedures and examinations is paramount to decreasing porosity concerns and ensuring the general top quality this website of welded joints.
Final Thought
To conclude, porosity in welding can be an usual issue that affects the high quality of welds. By recognizing the usual root causes of porosity and executing finest techniques for avoidance, such as correct welding techniques and testing steps, welders can make sure premium quality and reliable welds. It is important to focus on avoidance approaches to minimize the occurrence of porosity and maintain the integrity of welded structures.
Report this page